Hole Diameter is the actual diameter of the pellet. Typical hole diameters for various feeds vary according to the requirement, i.e. smaller for aquatic feed, a bit larger for poultry and cattle feed.
The effective length is the die thickness that actually performs work on the feed. More is the effective length more is the compactness of the pellet.
Total thickness is the overall thickness of the die. The overall thickness provides the necessary die material to avoid breakage.
1.4) Relief (Counterbore Depth) –Pellet Mill Die: (R)
The relief provides the way for the pellet feed, so that feed can easily come out from the pellet die. As shown in figure “ R” is the relief. Lesser is the Relief more compact is the pellet & more is the relief lesser is the pellet compactness. Relief varies in various patterns according to the requirement & feed formulation. Sometimes two specific outer rows are having more relief for uniform wearing as the compression by the roll shells on the outer rows is a bit less.
1.5) Inner Diameter of the Die–Pellet Mill Die (I.D.):
The inside diameter is the most common identifying dimension of a die and is always specified during die selection and equals to Outside dia. – (2 X thickness of die).
1.6) Overall Width of the Die–Pellet Mill Die (O.W.):
The overall width of a die may vary. Often, there is more than one width available for each die diameter according to the die category like standard die, extra-wide die.
1.7) Working Width–Pellet Mill Die (W):
Die working width is measured between the two inside edges of the die grooves. The die working area is the area inside of the two die grooves.
1.8) L/D Ratio–Pellet Mill Die:
The L/D ratio is the effective length (L) divided by the hole diameter (D). High L/d ratios provide high pellet die resistance as feed moves through the hole. Low L/D ratios provide low resistance as the feed moves through the hole.
1.9) Counter Sink Diameter – Pellet Mill Die:
The diameter of the inlet where the feed enters the compression area of the pellet dies. Different configurations of the inlet (countersinks, tapered inlets, well inlets, etc) can be used to achieve extra compression if needed for particular materials.
1.10) Inlet (well) depth –Pellet Mill Die:
The depth of the countersink is the inlet depth.
1.11) Degree of Countersink – Pellet Mill Die:
The degree of countersink also referred to as the choke. This degree is important as it determines the force to which the feed material is pushed into the pellet compression area.
4. Selecting Pellet Mill Dies for poultry, cattle & aqua feed.
Selecting a die as per formulation is very important. As Broiler contains fewer fibers and more oil %age (soft formulation), which provides better pelleting properties, less frictional load on pellet die. Hence, we can use a compression ratio of 1:12, 1:13 & even more.
Using a high compression ratio for layer feed may lead to poor die life, die chocking, non-uniform PDI, more power consumption in layer feed, low output, more wear & tear. (We can use 1:9 or 1:10)
And using low compression dies in soft broiler formulation may lead to poor PDI (Pellet Durability Index – Pellet Strength). Considering all the above factors using a separate die for both layer & broiler feed is a better and cost-effective solution.
Similarly for sinking aqua feed we need better water stability; hence it’s wise to use a high L/D Ratio of better PDI & good water stability.
5. L/D Ratio in pellet mill dies.
The L/D ratio is the effective length (L) divided by the hole diameter (D). High L/d ratios provide high pellet die resistance as feed moves through the hole. Low L/D ratios provide low resistance as the feed moves through the hole.
Example: Pellet Mill Die of 3 mm hole size with L/D ratio 1: 12 means, 12 ( working ratio ) multiply by hole size i.e. 3 mm = 12 x 3 = 36 mm ( working length)
6. Significance of Working or Effective Length in pellet mill dies.
The effective length is the die thickness that actually performs work on the feed. More is the effective length more is the compactness of the pellet & lesser the working or effective length low is the compactness or PDI.
But we cannot go beyond a certain limit while selecting working length for a pellet mill to die; increasing working length above a certain limit without knowing the other process parameters like grinding texture, oil & fibers content in the formulation may lead to poor die performance & chocking of pellet mill die.
7. Adjustment of the gap between the die & roller shells.
Follow the below steps to properly set/adjust the gap between the die and roller shells:
- Shut down the pellet mill
- Make sure that the eccentric shafts, clamps, bolts, and surfaces are clean so that rolls can be turned with ease.
- Clean the inside diameter of the die and outside diameter of roll shells.
- Be sure that there is no feed or dust between the rolls and the die and all surfaces are clean.
- Put a visiting card or paper folds (~0.5 mm) between the die and the roll shells.
- Adjust the roll until it is tight enough against the card so the roll shell cannot be turned against the die.
- Use the same procedure with other roll shells.
- After the rolls have been set up, check both rolls to ensure that they are tightened evenly.
8. Optimum life of pellet mill dies & roller shells.
Die is the most critical component of any pellet mill and also known as the heart of the pellet mill. It becomes very important for any pellet mill user to take maximum tonnage from a pellet mill with the required quality and reduce its cost per ton. Die life depends on a number of factors and we want to discuss the factors on which the life of die depends:
1.) Feed Formulation & composition: Formulations rich in fiber content are hard, thus pelleting is difficult and therefore the die life is less in this case. The life of dies used for producing layer feed (high fiber, less oil, Calcite) is very less as compare to broiler feed.
2.) Characteristics & Properties of the raw materials: Life of die also depends upon the characteristics of raw materials i.e. fibrous, spongy or dry, or good fat content. Raw materials containing marble powder/silica & other abrasive particles wear dies more rapidly.
3.) Fat content in feed: As good fat content in feed acts as a lubricant, therefore, a formula containing 1.5-4% fat runs smoother and is less abrasive due to less friction as the fat present in feed reduces friction.
4.) The particle size of the mash: A die-producing pellets from consistent particle size mash will give good life as compared to die-producing pellets from uneven and oversize of particle size of mash.
5.) Moisture content: A poorly conditioned mash also reduces the die life. Conditioning parameters play a very vital role in increasing die life.
6.) The skill of operator: The operator should regularly check the-
a. State of wear on the deflectors and scrapers and also the roll adjustment: To avoid uneven wear on the die and consequently inefficient pelleting.
b. The state of wear of the conditioner paddles: To ensure efficient pre-conditioning.
c. Steam traps and filters: To ensure that no condensate is being passed into the conditioner.
d. Press Roll slippage due to increased moisture content, it leads to die rollover.
7.) Changing Side of die: observing wearing pattern of die; it is recommended to change the side of the die (front side – Back side) for more uniform wear.
8.) Cleaning of magnets: It is recommended to clean magnets every 6 hours.
9.) Timely changing Roll Shells: It is recommended to use a minimum of 2 set rolls perdie.
10.) It’s recommended to tight roll shell support stud bolt timely.
Sometimes we use the consumable parts more than their standard life but lose much more in feed quality and life of other parts which directly relate to them. Like for an average die life cycle it is recommended to use a minimum of 4 pieces (2 sets) of roll shells for a better die life and uniform PDI feed quality. Hence using the roll shells & beaters more than their recommended life results in great losses in terms of grinding texture, conditioning, pellet quality, and specific energy consumption.
11.) Using the Same die for Broiler & Layer Feed: Broiler contains fewer fibers and more oil %age (soft formulation), which provides better pelleting properties, less frictional load on pellet die. Hence, we can use a compression ratio of 1:12, 1:13 & even more.
Using a high compression ratio for layer feed may lead to poor die life, die chocking, non-uniform PDI, more power consumption in layer feed, low output, more wear & tear.
And using low compression dies in soft broiler formulation may lead to poor PDI (Pellet Durability Index –Pellet Strength). Considering all the above factors using a separate die for both layer & broiler feed is a better and cost-effective solution. For Layer feed – The minimum hole size for the die should be or more than 3.5 mm.
Considering all the above factors it is very difficult to predict the actual life of the die, but under standard desirable factors, a die should minimum run approx. 600 to 800 hours.
9. Advantages of Stainless steel high chrome die over mild steel die.
1) In the case of S.S Die, the change in the size of the pellet from start to end of die is negligible, whereas in the case of M.S Die there is a huge difference in the pellet size from start to end. For example in the case of M.S., we start the die of 2.5 mm hole size and it ends with 3.0 mm or 3.2 mm, but in the case of SS die, if we start with 2.5 mm hole size, it will end with a 2.7 mm hole size maximum.
2) The life of S.S Die is approximately 3 times the life of M.S Die, which results in reducing the downtime of the plant and helps in increasing the capacity of the plant, and also helps in reducing the maintenance cost.
3) In the Case of S.S Die there is an immediate start-up with full production from the time of installation; But M.S Die initially required some time to start up with the full production, which ultimately affects the capacity of the plant.
4) Pellet made from S.S. Die has better strength as compared to that of M.S Die.
5) In the Case of S.S Die because of the longer working length, the retention time of mash with die is more, which results in the instant rise in temperature, which helps in gelatinization and reduces the bacterial load.
6) Problem of Choking the hole is less in our S.S. dies in the comparison of M.S. Dies.
10. Why stainless steel high chrome grade attracts magnet?
In order for an SS to be magnetic, a couple of requirements need to be met:
I. It must have iron in it.
II. It must have its crystal structure be arranged in ferrite or martensitic structure.
If an SS is mostly comprised of an austenite structure, then it will not be magnetic.
Now if we talk about X46Cr13, it has a martensitic structure and classifies as Martensitic stainless steel. Due to this reason, X46Cr13 attracts a magnet.
11. Can pellet mill die be repaired?
A die can be re-countered if the counters have worn out prematurely. It can be seen if the die working pad is not in the same plain as the depth of internal grooves, it can be re-countered.
12. Main reason for pellet mill die rollover.
Rollover is the condition of the die face when the hole inlets start to peen closed. If the rolls come into contact with the working surface of the die and damage it, laminating its surface and deforms the entrance of the holes. This peening action has disastrous effects on both pellet quality and the die throughput.
When does “rollover” arise?
When the rolls are too close to the die
When the wear ring (or clamping ring) has excessive play
When the main bearings of the die holder assembly have excessive play
What problems can “rollover” cause?
Inadequate production with the motor at full-load
Excess mill vibration & early breakdowns
13. Significance of PDI in Pellet quality.
Pellet quality is usually expressed as the Pellet Durability Index(PDI) and measured by using a tumbling device, in which the pellet sample to be tested is first sieved to remove fines, then tumbled in the tumbling can devise for a defined period of time. Then after tumbling we compare the fines produced during tumbling with actual weight.
PDI = weigh of the pellet after tumbling / weight of Pellet before tumbling x 100
At PDI lower than 85 pellets tend to break during crumbling; producing more fines which result in more recycling of feed and low final output.
14. Different types of relief used in pellet mill dies.
Enlarged holes are counter-bored into the die to reduce its working length and provide the proper compression ratio (L/D) while maintaining the total thickness needed to prevent die breakage. Specific rows of die holes, such as the two inner and outside rows, also sometimes are counter-bored to greater depths to encourage feed flow through these outer rows of holes to help dies wear more evenly, this is referred to as (VR) variable relief. Some examples of various die relief patterns can be seen in this diagram:
Types of relief:
1. NO RELIEF:
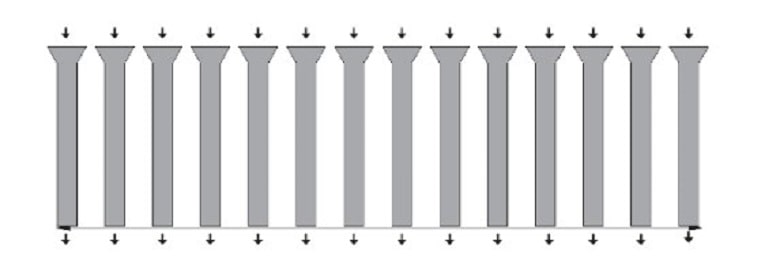
This means that the working length or effective length of the die hole is equal to the total thickness of the die. There is no relief present. Usually in dies that require very little total thickness, for example, sinking fish feed or shrimp feed dies.
2. STRAIGHT or SINGLE STEP RELIEF:
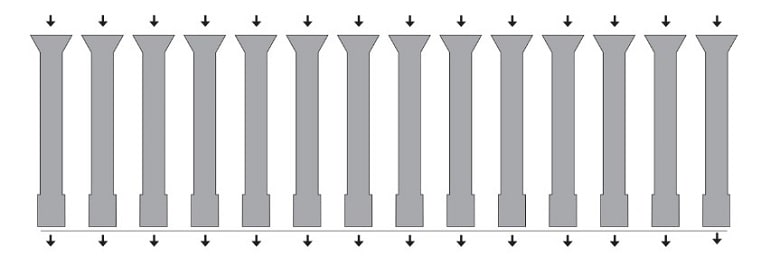
The relief is uniform across the die to obtain the desired effective thickness.
3. DUAL STEP RELIEF:
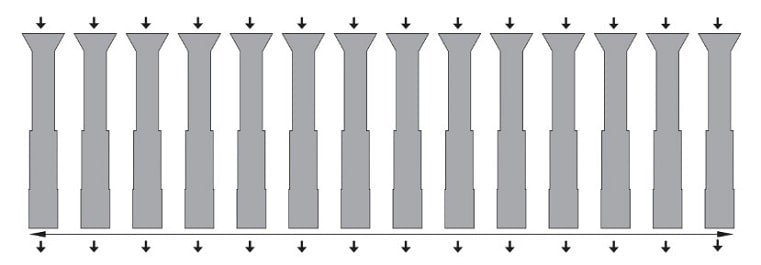
This type of relief is normally used in dies with large thickness to maintain the die strength along with the required ease of pelleting.
4. VARIABLE RELIEF:
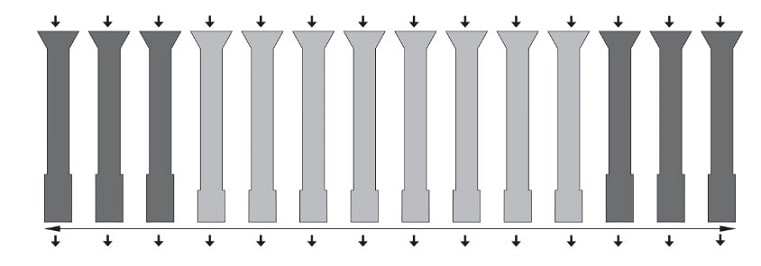
In this type of relief pattern, the relief on the outer rows is made deeper, reducing the working length of these rows. This is done to prevent uneven wear of die from the outer sides because the powder feed tends to escape from sides due to resistance offered during pelleting. Therefore the purpose is to encourage the pelleting evenly across the die.
5. STAGGERED RELIEF:
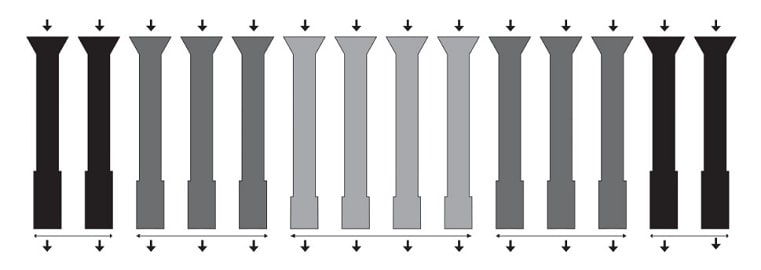
This is another type of variable relief. In this case, the relief of outermost is deepest, and then counterbore depth decreases towards middle lines. The purpose is the same as that of variable relief.
6. TAPERED RELIEF:
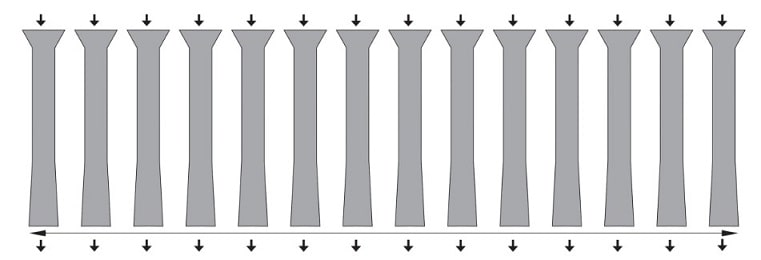
A tapered relief is used for special applications. Holes are gradually tapered out on the outside diameter of the die. It is used for spongy materials such as fish feed or alfalfa. The purpose of this relief is that when due to wear, the hole size enlarges thus decreasing the compression ratio, it is partially balanced by this taper.